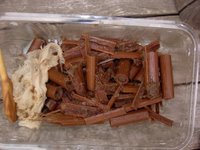
I started beating the pulp this afternoon. The easy way is to spend $7000.00 for an Hollander Beater - the alternative is to find a good pounding rock and beat by hand. I would dearly love one of these but until I win that zillion $$ lottery, it's the alternative for me. A good pounding rock is one that fits in the palm of your hands nicely. You may need to pound for hours and hours.
The rock pounding broke up the bigger chunks and I can use the mixer to break up the rest. The mixer resembles a modified paint stirer that you attach to an electric drill. As long as you're careful not to overheat the drill, it will do a pretty decent job of breaking up the fibres. Not practical if you're making paper on a large scale but good enough for the home hobbist like me. It's not a good idea to use it when the pieces are big as you don't want to chop up the fibre but to break it apart.
Day 6
Nothing new to report on the progress of the sunflower pulp. This is taking a lot longer than I anticipated. The pulp is S-L-O-W-L-Y breaking down. I can't beat it more than 15 minutes at a time because the drill will overheat.
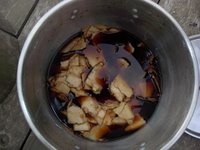
Cotton linters are made up of the very short fibres, the leftovers after the cotton plant has been processed for clothing fibres. The short fibres are pressed into 2'x 3' sheets, sold to papermakers. This fibre is even SHORTER than the regular cotton fibres we spin with. I have not tried spinning this stuff and will never ever attempt it. Might as well spin dust.
No comments:
Post a Comment